Benefits
of laser hybrid welding over conventional welding technologies
- Increase in welding speed (up to 3 times higher compared to submerged-arc welding)
- Significantly reduced heat input
- Reduction of the component distortion and thus the rework by 70%
- Environmentally friendly welding process with a very good eco-balance
- Increase in penetration depth
- High process stability
- High cost-effectiveness
- Low-spatter welding
- Less additive material
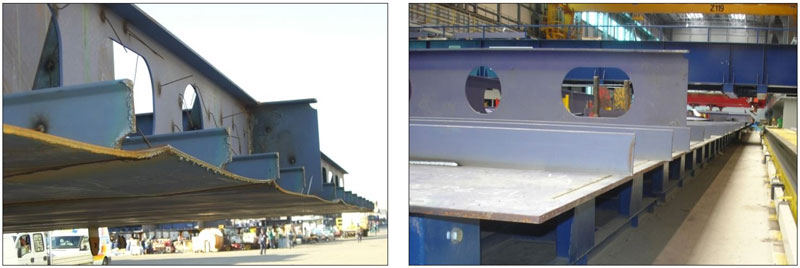
Comparison between a submerged-arc welded (left) and a laser-hybrid butt-welded (right) panel.
Outlook
and further development
With our research and development team, we are continuously working on the further development and perfection of laser hybrid technology and strive for the following advances and innovations:
- Increase of weldable plate thicknesses
- Expansion of the material range by 5000 and 6000 aluminum alloys and NIRO/stainless steel
- Transfer to other production areas, e.g.: beam production
- Establishment in the shipyard industry by reducing the necessary investment costs and operating costs